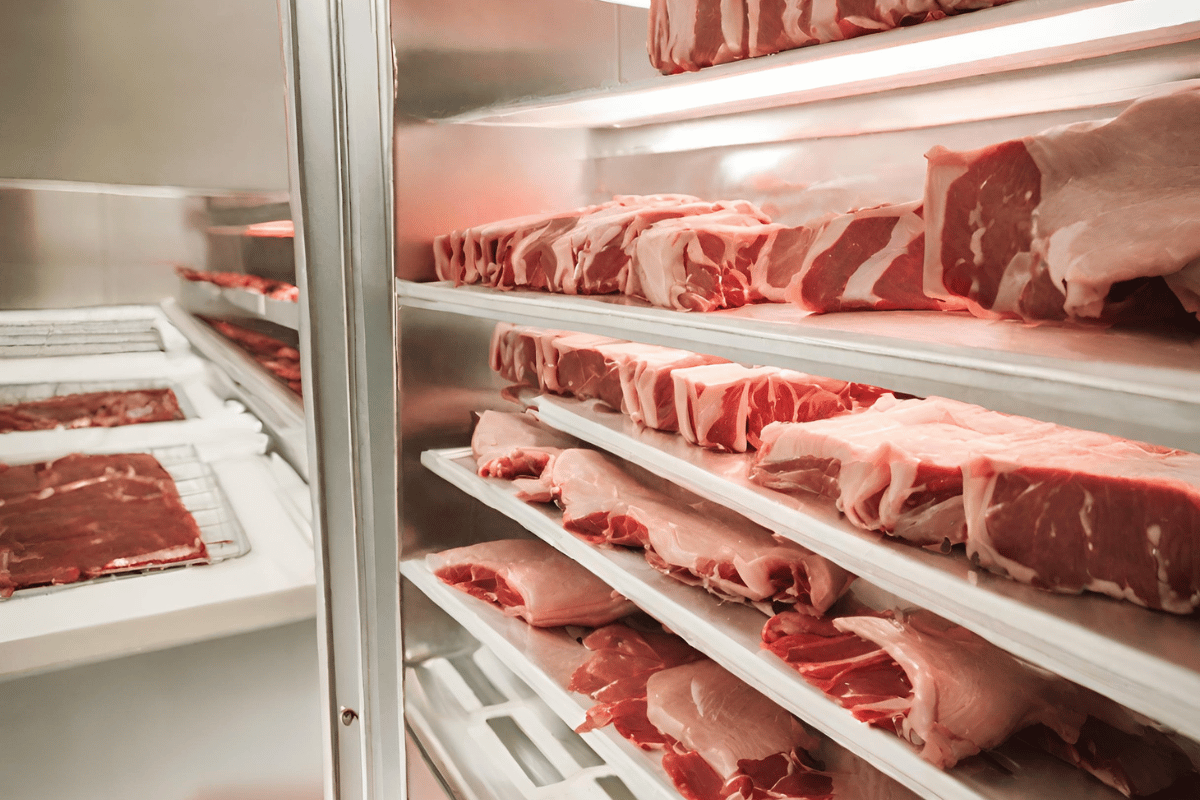
When looking for insulation for a walk-in freezer, cooler, or other commercial cold storage room projects, we tend to focus on two things; how to get it cold and how to keep it cold. These are obvious needs as they keep your product protected and your operation running smoothly, but in many cases, the insulation of your commercial cooler or freezer is regulated by the Department of Energy (DOE). This means the standard of your current insulation, and its continued performance are key to keeping you out of trouble and avoiding penalty fees.
What Are the DOE’s Regulations for Walk-In Coolers or Freezers?
It’s important to start this out with a disclaimer; we are not lawyers. However – because these regulations matter to our customers – they matter to us. If you would like the official documentation behind these rules, it can be found by visiting the Department of Energy’s website.
The DEO defines a Walk-In Cooler or Freezer as, “An enclosed storage space refrigerated to temperatures, respectively, above, and at or below 32 degrees Fahrenheit that can be walked into, and has a total chilled storage area of less than 3,000 square feet.” If this describes your project or your current space, these next few points are for you. If your facility is used for medical, scientific, or research purposes, you can rest assured these do not apply.
The R-value of the insulation for a commercial cooler (28° F and above) must be at least 25. The R-value of the insulation required for a commercial freezer (27° F and below) must be at least 32. These must be met for the lifetime of that cold storage facility. So, if years after the initial construction you experience damage – such as ice buildup in your walk-in freezer – you could be at risk of financial penalties if you do not take action.
How Lack of Proper Insulation Can Hurt Your Product
At Permatherm – we are involved and invested in the success of our customers, and it goes past the sale of insulated metal panels. Continuing engagement is one of “7 Uniques,” and something we take great pride in, even if the original product was not our own. Let’s take a look at what this means in the real world.
A contractor outside of Lexington, Kentucky, was facing a reputation-ending problem. A meat packing facility he’d overseen constructing several months prior was now failing. The insulation needed for their walk-in cooler was not holding up, causing extreme moisture accumulation and extensive food damage.
In just a few weeks, his client lost over 5,000 lbs. of choice, USDA grade beef, and almost $20,000 in unsellable inventory. They both needed solutions quickly. Fortunately, one of PermaTherm’s on-site consultants showed up within a week and helped them identify their problem and offer a solution. And because we boast of some of the fastest turnaround times in the industry, they were able to keep their business from hemorrhaging further.
If you were faced with a career-shattering construction failure – would you call for a consultation? This contractor did. With our panel consultants, you have access to over 30 years of experience and over 10,000 completed cold rooms.
Meeting Insulation Needs for a Walk-In Cooler or Freezer
Insulated metal panels offer a range of R-values that deliver superior insulating properties based on the thermal, operational, and regulatory needs of your cold storage facility. Our custom panel designs not only provide thermal resistance, but their R-values also stay consistent, decreasing complications with the DEO and your product.
We work directly with all our customers, which puts us (the Manufacturer) on job sites regularly. Whether it is pre-construction planning, pre-installation prep, post completion follow-up or troubleshooting problems from other competitors that didn’t live up to expectations, you can expect to see us. When you’re considering the insulation needed for a walk-in cooler, freezer, or any other commercial cold storage facility, reach out to our team of experts at 706-623-0530 or go to our contact page to get the conversation started.
Recent Comments